MICROSECTIONS
The terms microsections and cross-sections and metallography all refer to essentially the same process, which has been in use for a very long time. This metallurgist was first involved in preparation of metallurgical sections in 1979 while working as a Project Engineer for Northwest Technical Industries, which is now PA&E’s Bonded Metals Division. Metallographic cross-sections such as the one shown in Fig. A were prepared using standard metallographic practices to document the “wave pattern” and other features of the explosively bonded material.
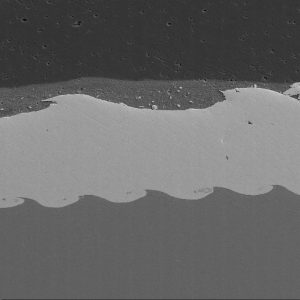
The same standard metallographic practices are used to microsection electronic components, printed wiring boards, solder joints, etc., which are typically combinations of metallic, ceramic, and polymeric materials. Some examples are shown below.
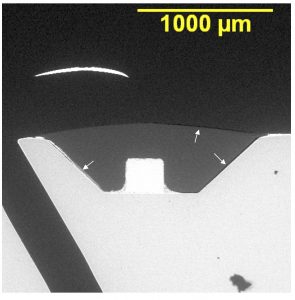
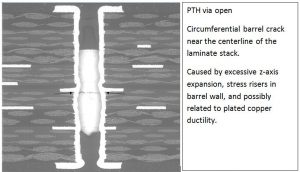
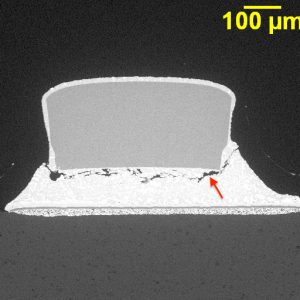
Preparation of microsections is more difficult for combinations of soft materials (metal & polymers) and hard materials (ceramic & semiconductors) because the soft materials polish at a faster rate than the harder materials. Nevertheless, it is worth the effort because root cause failure analysis often requires examination of microscopic material details such as microstructure, grain size, porosity, deformation, etc. that would be difficult or impossible to examine using other techniques. Measurements of solder joint height in microsections can be used to calculate the degree of thermal-mechanical warpage in a BGA assembly as illustrated below.
